In this blog, Gary Couling, Textile Fabrication Specialist at Moss, takes us on a journey throughout his three decades of experience in textiles!
“I’ve been working in the stitching and textiles industry for over thirty years now, and it’s been quite a journey. My early exposure to the industry came from working with my grandparents in Liverpool, where we manufactured industrial filters. This set my career in textiles before I knew it!
From Liverpool to Greece
After Liverpool and time living in New Zealand, I spent 18 years self-employed in Bicester as CEO at a company called TVT, where I got involved in some unique jobs.
One of the more interesting jobs was working on underwater concrete projects, including the second Severn crossing using Fabriform fabrics. I also had the opportunity to create a transport cover for the SS Thrust car and even made screens for the iconic Live Aid concert. My work took me to many places, and I am an avid traveller, often driving abroad. In recent trips, I’ve logged 4,000 miles – including visiting my daughter in Greece!
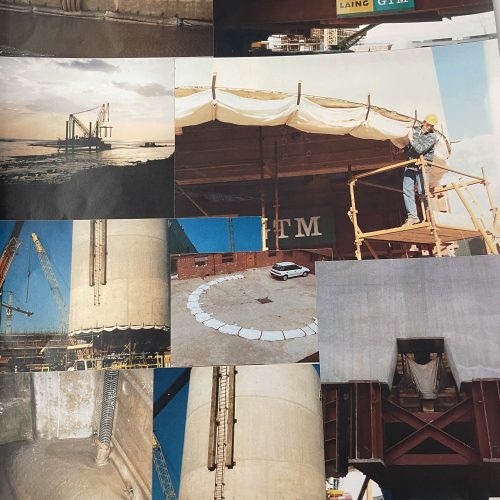
Second Severn Crossing, Bristol. 1993.
Stitched Fabric Formwork filled with concrete underwater to provide a seal before backfilling caisson.
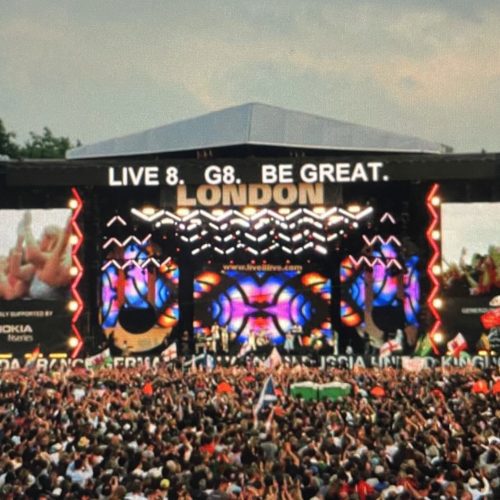
Live 8 Hyde Park London July 2005
Welded and stitched stage scrims.
Crafting Careers
In 2010, I started my career at Moss, although I’d had a prior relationship with the company while I was self-employed. Moss had a sewing machine at the time, but it was an old piece of equipment and needed upgrading. I saw an opportunity and helped establish the stitching department within the business. Initially, I brought in my own sewing machines and equipment to get things rolling, it’s amazing to think of the changes since then.
Our department now operates with a variety of machines to tackle many different tasks, such as medium to heavyweight fabrication, Keder finishing, stitching Velcro and hems. Accuracy is crucial, especially with dye sublimation processes where matching images perfectly is essential. I’ve always emphasised the importance of guides and skills to ensure efficient operation and to avoid defects. Visual inspections are a key part of our quality control, and the team is responsible for handling and correcting any issues that arise. If errors are made, the team know they can come to me. I’ve picked up a few tricks over the years to help with mistakes, and I’m always ready to lend a hand when needed.
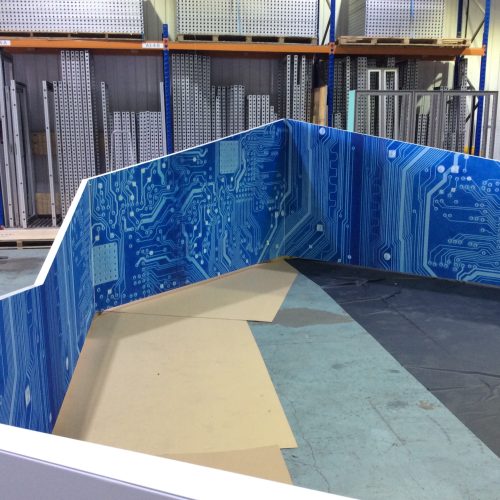
Moss UK
Angled tension fabric, fabricated in six sections with flowing image.
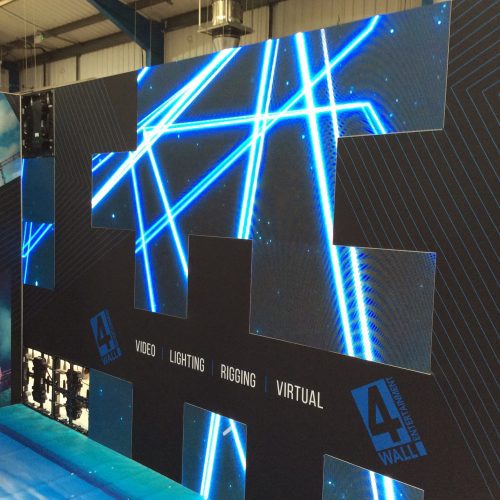
Moss UK
LED and Fabric Wall. Single piece tensioned fabric.
Behind the Thread
Our team of five operates across two shifts, from 6am to 10pm, ensuring we meet even the most challenging of deadlines. Our scheduler knows the workload our department can handle and manages it well, so we can work in tandem with other departments’ needs. I’m incredibly proud of how far we’ve come. The team is young, enthusiastic, and knowledgeable, and I take great pleasure in helping them and sharing my knowledge. At Moss we embrace a “One Company” mentality, working together to achieve our goals and I would like to think our team does exactly that.
We handle 10-15 different substrates, each with unique handling requirements. For outdoor works like flags, we need a ‘belt and braces’ approach to ensure durability against the elements. For indoor installations, like retail setups, it’s all about achieving the perfect look, so you have to tailor your fabric selection according to the task at hand. While lighter modern fabrics are preferred over heavier PVC materials, working with PVC requires a certain level of strength to push it through the sewing machine. One of my favourite projects was a video wall with LED panels and fabric infills. The fabric had to be one continuous piece, which was quite the challenge, but I really enjoy working on challenging and complex shapes.
Of course, there are challenges. Maintaining straight stitches, especially with large panels, can be tricky. It can also be tiring work, so it’s essential to remain mentally sharp. I’ve had my fair share of incidents when I was self-employed while working when tired, including stitching my finger three times! At Moss, we make sure these situations could never arise, as safety is of paramount importance to our business.
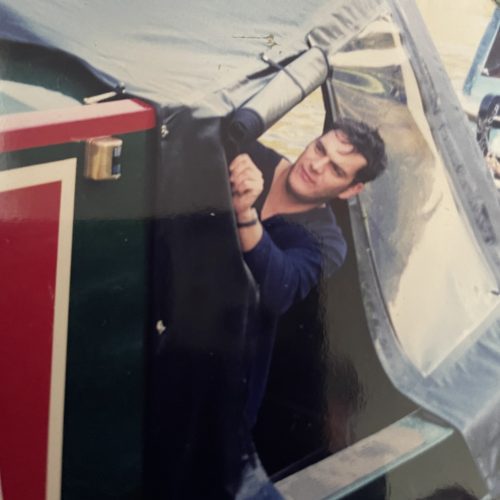
Marine Cover
Three Decades in Textiles
Reflecting on my career, I am proud of the diverse experiences and unique challenges I have undertaken. From working with my grandparents in Liverpool to setting up the stitching department at Moss and seeing it thrive, I’ve always been driven by a passion for textiles and stitching. The industry has evolved significantly over the years, and I’ve been fortunate to be a part of that journey.
Being part of such a talented team at Moss, I look forward to tackling new projects and pushing the boundaries of what we can achieve in creating spectacular experiences for our clients. Here’s to many more years of stitching together, one thread at a time!”